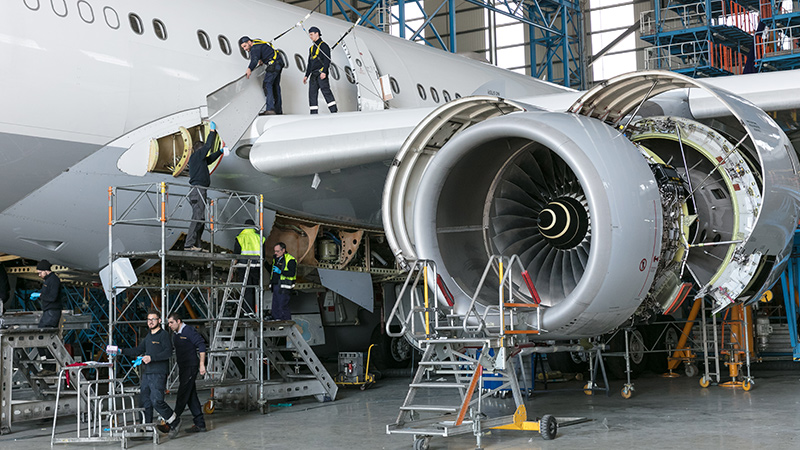
In the aviation industry, predictive maintenance (PdM) is applied across various systems and components to ensure operational efficiency, safety, and cost-effectiveness. Below is a comprehensive list of the key areas where predictive maintenance is required in aviation:
1. Engine Maintenance
- Engine Performance Monitoring: Monitoring parameters such as temperature, vibration, pressure, and fuel consumption to predict potential failures, wear, or efficiency losses.
- Compressor and Turbine Health: Sensors track wear on compressors, turbines, and other internal components, predicting when they may require servicing or replacement.
- Oil and Fluid Monitoring: Real-time analysis of oil pressure, temperature, and contamination levels can predict when oil changes or repairs are needed.
2. Landing Gear Systems
- Shock Absorbers and Struts: Predictive maintenance can detect wear on landing gear shock absorbers and struts, which are critical for safe landings.
- Braking Systems: Monitoring the condition of brake pads, discs, and hydraulic systems, predicting when components will need to be replaced or serviced.
- Wheel and Tire Condition: Sensors track tire pressure, temperature, and wear, helping to predict failures and optimizing tire replacement cycles.
3. Avionics Systems
- Flight Control Systems: Monitoring the health of flight control actuators, autopilot systems, and sensors that ensure accurate flight control.
- Navigation and Communication Systems: Predicting failures in avionics components such as GPS, radar, and communication equipment to prevent disruptions in operations.
- Electrical Systems: Monitoring battery performance, power distribution, and wiring systems to avoid electrical failures that could affect multiple systems.
4. Hydraulic Systems
- Hydraulic Pumps and Valves: Sensors in hydraulic systems predict failures in pumps, valves, and actuators, which are critical for controlling flight surfaces, landing gear, and brakes.
- Fluid Pressure and Contamination: Tracking the pressure and contamination levels in hydraulic fluids to predict when maintenance is needed.
5. Fuel Systems
- Fuel Pumps and Filters: Monitoring fuel pumps, fuel lines, and filters to ensure optimal performance and detect potential failures in the fuel delivery system.
- Fuel Tank Sensors: Predicting failures or leaks by analyzing pressure and temperature data within the fuel tanks.
6. Cabin Systems
- Air Conditioning and Environmental Control: Predictive maintenance ensures optimal functioning of air conditioning units, cabin pressure systems, and environmental controls, identifying potential issues like refrigerant leaks or failing compressors.
- Oxygen Systems: Monitoring oxygen generation and distribution systems to ensure they are functioning correctly, particularly in case of emergency.
7. Structural Components
- Airframe Monitoring: Continuous monitoring of stress, vibration, and fatigue data from various parts of the airframe, including wings, fuselage, and tail, to predict structural weaknesses or damage.
- Corrosion Detection: Predicting corrosion or material degradation in high-stress areas through sensors that track environmental factors such as humidity, temperature, and saltwater exposure.
- Fatigue and Stress Monitoring: Sensors that measure structural stress and fatigue on the airframe and critical components, ensuring that parts are replaced or repaired before failures occur.
8. Electric and Power Generation Systems
- Generators and Alternators: Monitoring the performance of onboard power generation equipment to predict failures or degradation.
- Battery Health: Predicting when aircraft batteries, including auxiliary power units (APUs) or emergency batteries, are approaching the end of their lifecycle.
9. Aircraft Systems
- Windshield Wipers and De-Icing Systems: Predicting failure in critical safety components such as windshield wipers and de-icing systems that are vital in adverse weather conditions.
- Flap and Slat Systems: Monitoring the condition of flaps and slats for wear or malfunction, which could affect aerodynamics during takeoff, flight, or landing.
10. Aircraft Cabin and Seating
- Seat Systems: Predicting failures in seats, including malfunctioning recliners or seatbelt systems, which are crucial for passenger safety and comfort.
- Cabin Lighting: Monitoring the condition of lighting and emergency signaling systems within the cabin, ensuring they remain functional.
11. Auxiliary Power Units (APU)
- APU Health Monitoring: Monitoring temperature, vibration, and fuel consumption to predict potential failures in the APU, which is crucial for providing electrical and pneumatic power while on the ground.
12. Maintenance and Inspection Scheduling
- Inspection Management: PdM tools help schedule and optimize inspections based on real-time data, reducing unnecessary maintenance and downtime.
- Part Lifespan Predictions: Predictive models estimate when parts (e.g., filters, seals, bearings) will reach the end of their useful life, allowing maintenance teams to replace parts before they fail.
13. Wings and Control Surfaces
- Surface Defects and Deformation: Monitoring the condition of wings, flaps, ailerons, and other control surfaces for early signs of wear, cracks, or deformation.
- Hydraulic Actuators: Predictive maintenance of hydraulic actuators used for controlling flight surfaces ensures timely repair or replacement, avoiding control issues.
14. Environmental Monitoring Systems
- Weather Sensors: Predicting failure in onboard weather radar, wind shear sensors, and other environmental systems, which are essential for safe navigation, especially during adverse weather conditions.
15. De-Icing and Anti-Icing Systems
- Ice Protection Systems: Monitoring the health of systems that prevent ice buildup on aircraft, such as wing and tail de-icing systems, and predicting when maintenance or fluid replacement is necessary.
16. Communication and Monitoring Systems
- Real-Time Monitoring Systems: Aircraft’s communication systems that interact with the airline’s maintenance management system for continuous health monitoring of the fleet.
Predictive Maintenance Technologies Used in Aviation:
- IoT Sensors: Embedded sensors collect data on various aircraft systems in real time.
- Machine Learning (ML) Algorithms: Analyze data trends and patterns to predict failure before it occurs.
- Big Data Analytics: Manage and process large datasets from multiple aircraft and sensors.
- Cloud Computing: Store and access data remotely for real-time analysis and fleet-wide predictive maintenance.
- Digital Twins: Virtual replicas of aircraft systems that simulate and predict maintenance needs.
- Artificial Intelligence (AI): Used to identify complex patterns in vast datasets, improving predictive accuracy over time.
Conclusion:
Predictive maintenance in aviation spans across virtually every major system of the aircraft, from engines to avionics to landing gear. By continuously monitoring these systems, predictive maintenance helps detect early signs of wear or failure, improving safety, reducing downtime, optimizing maintenance schedules, and lowering operational costs. As technology advances, the scope and effectiveness of predictive maintenance in aviation will continue to grow, offering even more sophisticated capabilities for fleet management and aircraft health.